NELL’AZIENDA LECOFER CON SEDE IN SICILIA, (ALCAMO, PROVINCIA DI TRAPANI) RIMOR CAMIT HA INSTALLATO UNA GRANDE CABINA DI GRANIGLIATURA E UNA DOPPIA CABINA-FORNO PER L’APPLICAZIONE DI CICLI PROTETTIVI ANTICORROSIVI.
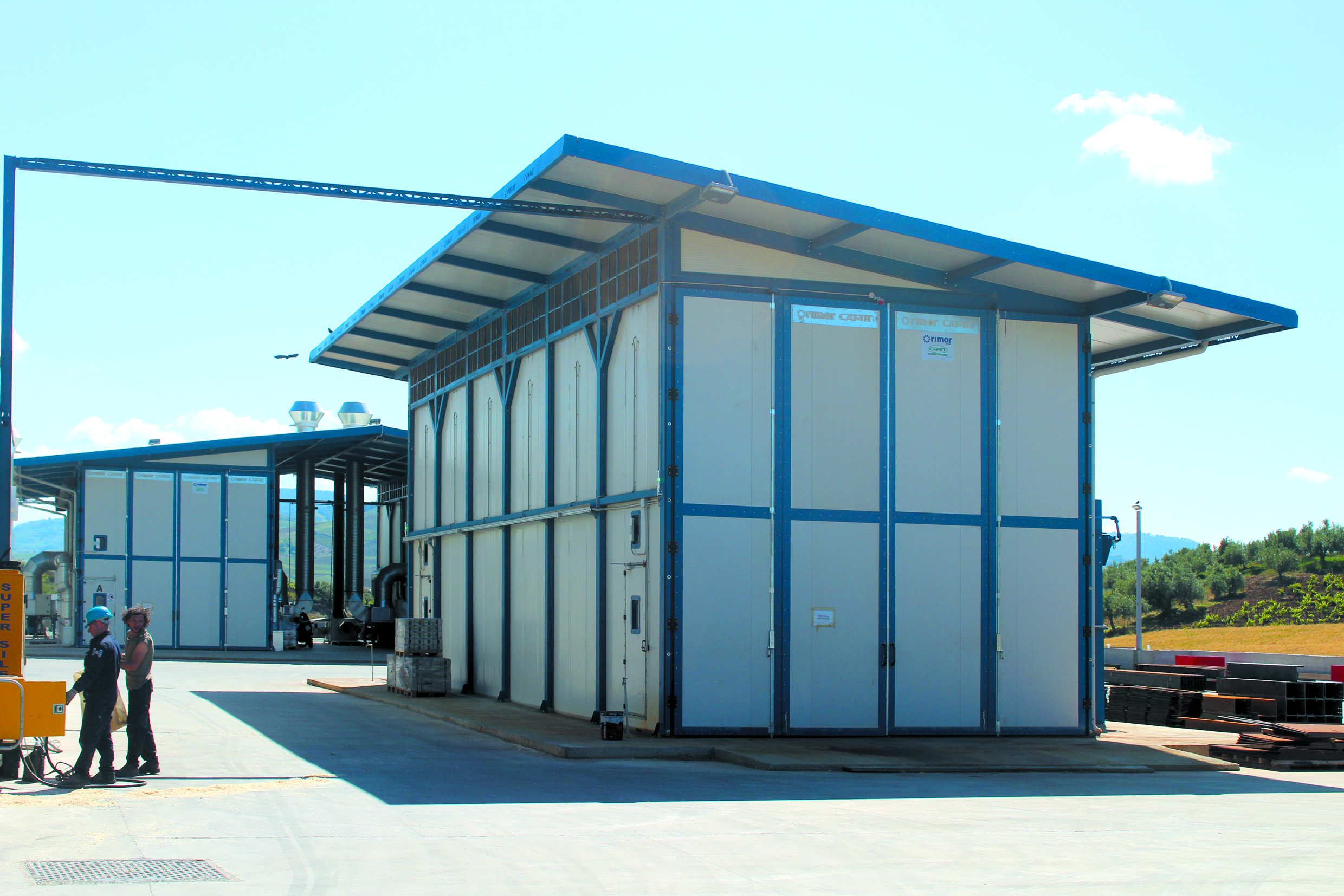
Lecofer è l’azienda del gruppo Milotta che si dedica alla trasformazione metallica per la produzione di carpenterie e costruzioni metalliche civili e industriali. Il gruppo ha attività che spaziano dall’edilizia ai legnami, dalla ferramenta alla termoidraulica e all’industria fotovoltaica. La sede Lecofer di Alcamo (Trapani, Italia) occupa 70.000 m2. Vi lavorano ingegneri, disegnatori, saldatori e carpentieri specializzati, responsabili qualità e controllo processi. Al loro fianco, la squadra di progettisti offre container per l’installazione di componenti elettrici ed elettronici, inverter, trasformatori, generatori elettrici e, chiavi in mano, strutture e telai per impianti fotovoltaici.
La sede visitata, diretta da Antonino Cipolla, è in fase di ulteriore implementazione. Il reparto di preparazione delle superfici è già perfettamente attivo. Consta di una grande cabina di granigliatura e una doppia cabinaforno per l’applicazione dei cicli protettivi, progettati, fabbricati e installati da Rimor Camit.
Accompagnati da Antonino Cipolla e Roberto Carrieri (Rimor Camit), abbiamo visitato il reparto, installato all’aperto, a fianco dei due grandi capannoni di produzione, che lavorano a flusso.
«Siamo specializzati nella lavorazione di differenti metalli – spiega Antonino Cipolla – acciaio inox, corten, lamiere e ferro. Progettiamo senza nessun limite imposto da forme particolari o difficoltà di realizzazione. Possiamo realizzare carter, tramogge, vasche a tenuta, serbatoi, o costruire basamenti, intelaiature, supporti, soppalchi, piattaforme, scale, tubazioni, interi capannoni, impianti oleodinamici, impianti scarrabili, compattatori e così via».
«Attualmente il nostro prodotto principale è costituito dai container – continua il nostro interlocutore – che progettiamo e fabbrichiamo su misura. La filosofia costruttiva è originale, sono strutture che assembliamo a partire da alcuni diversi modelli di basamento (che chiamiamo skid), con o senza vasca di sicurezza a tenuta stagna e separatore acqua/contaminanti, su cui vengono imbullonati montanti e traverse fabbricati su misura, tamponature e così via. Come in genere tutta la nostra produzione, eseguiamo tutte le fasi della progettazione, dai calcoli strutturali alla modellazione 3D all’industrializzazione del progetto, fabbricazione, assemblaggio e applicazione del ciclo protettivo (con esclusione della zincatura a caldo) e di finitura».
«La linea di produzione container oggi ha saturato le nostre capacità produttive: ne fabbrichiamo almeno 100 ogni mese. Per questo, prima dell’estate installeremo due nuove grandi macchine automatiche di taglio e conformazione sia delle lamiere sia delle travi, per poter servire con la necessaria flessibilità il mercato.
Per poter ottenere la capacità produttiva richiesta abbiamo organizzato il flusso di produzione mediante isole di lavoro in successione, servite da carroponti, e un magazzino di stoccaggio dei semilavorati (lamiere e travi tagliate, forate, piegate, filettate, e così via) all’esterno dei nostri attuali due capannoni [un terzo, che servirà la logistica delle materie prime in ingresso, è in fase finale di costruzione, così come i nuovi uffici, ndr], pronti per essere inviati alle isole di montaggio secondo il programma di produzione giornaliero. Da qui anche la scelta, il dimensionamento e la collocazione del reparto di preparazione e verniciatura delle superfici. Monitoriamo il progetto dalla fase di acquisizione fino al collaudo finale. Enti terzi, DNV e SGS, ci hanno rilasciato una serie di certificazioni, generali e specifiche per tipo di prodotto.
In particolare:
- ISO 9001
- centro di trasformazione (N. 3579/19) e sagomatura ferro per C.A.
- carpenteria metallica, Container Sea Version (DNV)
- carpenteria metallica – realizzazione di componenti strutturali metallici d’acciaio
- EN1090-1:2009
- EN1090-1:2009/AC:2010
- EN1090-1:2009+A1:2011
- ISO 3834-2:2005 – Carpenteria metallica strutturale per la realizzazione di opere civili ed industriali».
PRETRATTAMENTO E VERNICIATURA
«Data l’ampia gamma di prodotti – prosegue Antonino Cipolla – l’impianto di verniciatura è stato pensato per poter soddisfare tale grande varietà. Utilizziamo differenti cicli, su specifica dei clienti o nostro suggerimento. I container hanno destinazioni d’uso e geografiche diverse. Per quanto riguarda le destinazioni d’uso, abbiamo modelli che servono parchi fotovoltaici – in questo caso, contengono trasformatori ed inverter – oppure contengono pacchi batterie per l’accumulo d’energia o ancora, generatori elettrici di sicurezza o altre macchine che, di solito, sono installate all’aperto e quindi richiedono una protezione anticorrosiva molto elevata. Il numero importante di container che produciamo lascia intendere che il nostro principale cliente invia internazionalmente il prodotto finito e, dunque, deve resistere perfettamente al loro trasporto (il sistema tipico è via nave, i container, che contengono sistemi che pesano fino a 25 t, devono poter essere sovrapposti, fino a 10, e ovviamente resistere al peso e ai movimenti ondulatori della nave) e all’ambiente di destinazione, che può essere molto severo, sotto il profilo corrosivo».
CICLI APPLICATI
«Applichiamo cicli C4H, secondo ISO 12944: granigliatura con graniglia metallica angolare fine, 2 mani di fondo epossidico, 2 mani di finitura poliuretanica (spessore minimo di 260 μm). Le temperature operative delle cabine sono regolate automaticamente in un intervallo di temperatura ottimale sia per gli operatori, sia per l’essiccazione nei tempi corretti dei prodotti applicati. Recentemente abbiamo introdotto anche una linea di container zincata a caldo, che ha liberato una parte del reparto verniciatura (non quello di granigliatura: diamo allo zincatore un prodotto che ha già subito un primo trattamento meccanico di omogeneizzazione delle superfici), inoltre insieme alla zincatura sempre più spesso ci viene richiesta anche una finitura, e dunque abbiamo sviluppato anche cicli per lo zincato a caldo, con una fase di leggera granigliatura per l’eliminazione dell’ossido bianco».
«Ai container sono di solito abbinati armadi elettrici, cabine di trasformazione e altri componenti, che pure fabbrichiamo e verniciamo con i cicli anticorrosivi adeguati».
IMPIANTI
«Le cabine/forno sono lunghe 18.000 x 6.000 x 6.000 mm. Sono parzializzabili. Nascono per poter verniciare contemporaneamente 2 container da 20 piedi (o uno da 40 piedi) in ciascuna cabina-forno. Sono cabine passanti, per produrre a flusso. La cabina di granigliatura ha la stessa dimensione di ciascuna cabina/forno, anche in questo caso per trattare contemporaneamente 2 container da 20 piedi oppure 1 da 40».
DETTAGLIO TECNICO DEL REPARTO
«Il recupero e la selezione della graniglia – interviene Roberto Carrieri – si effettua con un sistema brevettato da Rimor Camit, operante ad aria e non meccanicamente. Il sistema si mette in funzione quando necessario (il deposito di graniglia e l’aspiratore gestiscono 4 tonnellate di graniglia alla volta), normalmente ogni 4-6 ore. Sia la cabina di granigliatura pneumatica, sia le cabine/forno sono state progettate previa simulazione fluidodinamica (per elementi finiti). La simulazione fluidodinamica ci permette di fare le opportune valutazioni relative all’omogeneità dei flussi d’aria, per migliorare le condizioni di lavoro per gli operatori (velocità verticale di 0,5 m/s) e offrire un ambiente adatto all’applicazione, in ogni zona delle cabine. Inoltre, permette di ottenere una minore sollecitazione dei motori e di evitare i picchi dei bruciatori. Se ne ha pure un vantaggio in termini energetici».
«Per le cabine/forno – prosegue Roberto – abbiamo installato bruciatori a GPL (nella zona d’installazione non esiste la rete gas). Il sistema di riscaldamento è a vena d’aria indiretta, una soluzione che consente sia di ottimizzare i consumi energetici, sia di proteggere la salute dei lavoratori. I flussi d’aria sono garantiti dall’aspirazione laterale dal basso. Il motore dell’aspiratore è montato in verticale con un fissaggio elastico che consente di minimizzare il rumore e allungare la vita utile dei motori (fino a 8 volte la vita utile dello stesso motore installato in postazione fissa orizzontale). È una soluzione brevettata da Rimor Camit, denominata “Recube”. L’intero sistema è gestito automaticamente, si autoregola in funzione della progressiva saturazione dei filtri».
«L’immissione dell’aria calda – continua Roberto – viene effettuata dall’alto mediante distributori rastremati, disegnati appositamente secondo quanto definito mediante simulazione fluidodinamica, così come il grado d’inclinazione del tetto e l’accesso del ricambio aria – trattata mediante filtrazione passiva (contrariamente ai sistemi con plenum orizzontale, nel nostro caso non ci sono ventilatori di spinta, l’aria viene richiamata dall’aspirazione inferiore laterale) -, e il posizionamento dei ventilatori (agitatori) verticali. L’insieme di queste misure – sottolinea Roberto – consente di avere una distribuzione perfettamente omogenea dei flussi d’aria diretti verso il basso all’interno delle cabine/forno, con cabina/ forno parzializzata o completamente in funzione e inoltre garantisce il funzionamento lineare del motore d’aspirazione, che si autoregola in funzione del progressivo intasamento dei filtri d’immissione dell’aria fresca. Se e quando fosse necessario aumentare le temperature per accelerare l’essiccazione dei prodotti applicati, in assenza di personale, il sistema si autoregola (riduzione delle velocità d’aspirazione, aumento dell’ingresso di aria calda), secondo quanto pre-programmato. Tutti i dati relativi alle cabine sono immediatamente messi a disposizione della direzione dell’azienda e del nostro ufficio d’assistenza tecnica, mediante connessioni digitali allarmate».
«Naturalmente – conclude Roberto – tutte e 3 le cabine sono state progettate per operare all’esterno, in qualsiasi stagione e situazione meteorologica. Gli unici lavori edili necessari per la loro installazione sono relativi alla predisposizione del plateatico, che deve avere il grado d’inclinazione minimo necessario per il deflusso della dell’acqua piovana».
CONCLUSIONI
«Abbiamo pensato il reparto di granigliatura e verniciatura prima della progettazione dei container zincati a caldo – conclude la visita Antonino Cipolla – tuttavia aver liberato le cabine/forno di una parte del lavoro ci permette quella flessibilità che attendiamo avere anche nel reparto di trasformazione mediante l’installazione delle nuove macchine. In definitiva, siamo convinti di avere effettuato la scelta ottimale per quanto riguarda protezione e finitura: i sistemi si gestiscono automaticamente, si controllano in ogni momento anche da remoto, il flusso di lavoro si conclude in modo efficiente tenendo traccia delle attività effettuate, nei tempi e con la qualità ottimale per la nostra produzione attuale e per quella che contiamo poter effettuare nel prossimo futuro».