L’IMPREGNAZIONE SOTTOVUOTO DI PEZZI OTTENUTI DA FUSIONE E PRESSOFUSIONE È UN NOTO PROCESSO CHE PERMETTE DI ELIMINARE, SIGILLANDOLI, ALCUNI DIFETTI TIPICI. NONOSTANTE I PROGRESSI CHE SI OTTENGONO ANNO DOPO ANNO, INFATTI, NON SI È ANCORA RIUSCITI A ELIMINARE COMPLETAMENTE IL FENOMENO DELLO SVILUPPO DEI GAS CHE FUORIESCONO DALLA MATERIA, GENERANDO MICRO CANALI E POROSITÀ, CIECHE O PASSANTI, CHE POSSONO INFICIARE LA FUNZIONALITÀ DEL PEZZO.
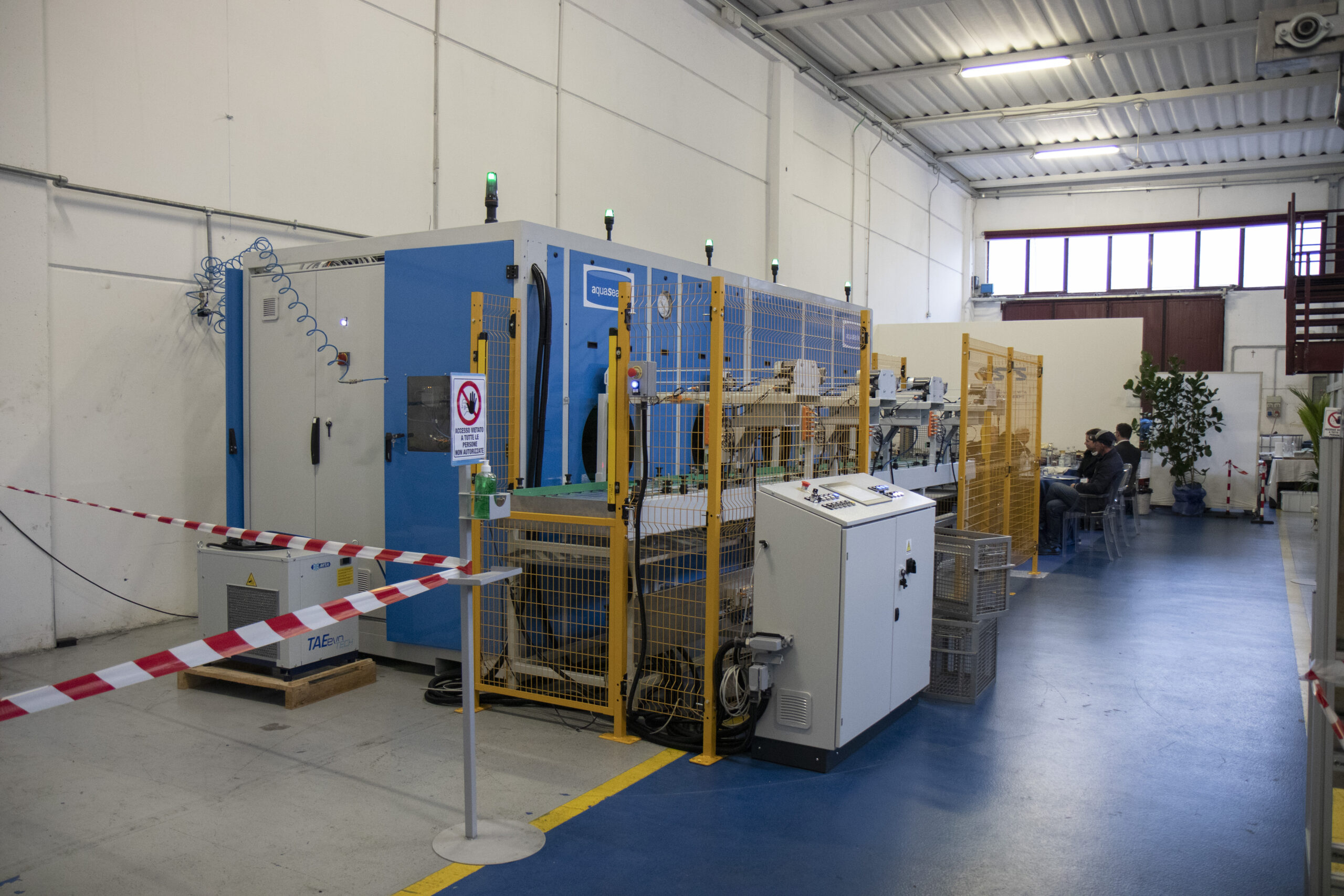
Con il progressivo e continuo aumento dei requisiti minimi di qualità specificati, un pezzo con porosità viene considerato scarto in campi sempre più estesi, anche laddove non ne siano inficiate le prestazioni tipiche (come invece accade per valvole, rubinetti, componenti di motori termici, oleodinamica e meccatronica). Le porosità generano normalmente crateri nel rivestimento – si generano nelle fasi finali del processo di verniciatura, in forno d’essiccazione/ polimerizzazione, o nella deposizione di rivestimenti inorganici (nichel chimico o nichel- cromo) – difetti che possono dare origine all’accelerazione dei fenomeni corrosivi, oltre che un aspetto estetico non accettabile. Per risolvere l’insieme di questi problemi, i pezzi di scarto (prima delle operazioni di rivestimento finale, se questo fosse il caso) possono essere recuperati mediante l’impregnazione sottovuoto con resine specificamente formulate. Le prestazioni dei relativi processi sono specificati da standard internazionali utilizzati in campo militare (per esempio, MILSTD 2764 e MIL I 17563).
Lo stato dell’arte della relativa tecnologia è stato recentemente presentata da STS, nel suo laboratorio di Ravenna (Italia), durante diverse sessioni di lavoro che hanno coinvolto, in due giorni, più di 50 aziende operanti nell’ambito della trasformazione metallica e dei servizi di impregnazione per conto terzi.
Il lettore interessato può vedere QUI la presentazione completa di Giorgio Cisotto, conosciuto tecnologo dei processi d’impregnazione e product manager STS per il settore.
IMPIANTO E PROCESSO
Aquasealer® RS è il marchio che identifica la gamma degli impianti STS per l’impregnazione sottovuoto. Il workshop nella sede STS è stato effettuato utilizzando una macchina (RS40) completamente automatica a 4 fasi (e 4 ceste portapezzi) operanti contemporaneamente. Come tutte le macchine e gli impianti STS – secondo la filosofia progettuale di Ciro Poggioli, il direttore generale dell’azienda – anche quelle della serie Aquasealer® RS lavorano al minimo impatto ambientale:
- senza produrre reflui (i formulati nanotecnologici di lavaggio a base bicarbonato e senza tensioattivi separano istantaneamente i materiali organici asportati. Nel caso del processo qui visto, si recupera quasi totalmente (almeno l’85%) la resina impregnante in eccesso
- senza produrre emissioni (le emissioni di vapore acqueo sono condensate, si recuperano acqua e calore).
Nella prima stazione, una volta introdotto il cesto (automaticamente) nel tamburo, si effettua un ciclo di vuoto secco seguito da vuoto umido e successiva centrifugazione, per recuperare l’eccesso di resina termoindurente (a base acquosa). Terminata l’operazione d’impregnazione (i tempi sono stabiliti dal produttore della resina) il cesto viene quindi traslato e immesso nella seconda stazione.
Qui si effettua un primo lavaggio, con formulati nanotecnologici a bassissima concentrazione – a base bicarbonato, senza tensioattivi – in acqua demineralizzata (per garantire il recupero pressoché totale della resina eliminata), con funzione antiossidante.
Un secondo lavaggio demineralizzato di finitura permette di ottenere porosità completamente impregnate e superfici perfettamente pulite.
La quarta stazione effettua la polimerizzazione finale della resina in acqua calda a 90 °C, seguita da una centrifuga a secco, sfruttando il calore residuo dei pezzi per l’asciugatura. Tutte le fasi sono effettuate a immersione, con cesta in rotazione (oraria e antioraria), tempi ciclo completamente programmabili in funzione dei materiali, della geometria dei pezzi trattati e della natura della resina impregnante, nei limiti prescritti dalla norma MIL 276/A.
Nel video è possibile visualizzare le diverse fasi di processo via simulatore.
DIBATTITO E CONCLUSIONI
La formula del workshop ha permesso ai presenti di approfondire con i tecnici dell’azienda diversi aspetti operativi, economici e ambientali. Sinteticamente: i diversi impianti Aquasealer® RS sono gestiti da PLC, consegnati con software di gestione pre-programmato secondo le esigenze di ciascuna azienda utilizzatrice (e le specifiche dell’impregnante utilizzato); quando necessario, i parametri sono facilmente modificabili mediante HDMI (interfaccia grafica touch d’immediata comprensione); l’interfaccia permette di controllare visivamente l’andamento delle varie fasi e utenze del processo; il software è interfacciabile al sistemi IT di fabbrica e garantisce la completa tracciabilità del processo.
Gli impianti sono dotati di tutti i sistemi necessari per lavorare a ciclo chiuso: recupero e filtrazione della resina; recupero e riutilizzo dei bagni di lavaggio e risciacquo che, lavorando per separazione fisica, non necessitano di ricambio, se non in occasione degli interventi periodici di manutenzione ordinaria delle vasche, che si effettuano in intervalli di tempo molto lunghi; i formulati di lavaggio e risciacquo lavorano a temperatura ambiente; il bagno di polimerizzazione è riscaldato elettricamente e si recupera sia il vapore acqueo, sia il calore residuo, mediante sistema di condensazione (non sono necessari né previsti camini d’espulsione vapore); l’alimentazione delle varie stazioni e il trasporto delle ceste portapezzi tra di esse sono gestite da rulliera automatica. Il trasportatore a rulli è configurabile, secondo le necessità del cliente, per gestire contemporaneamente da 2 ceste portapezzi a crescere (nella configurazione del workshop, 4 ceste attive, 2 al carico e 2 allo scarico).
Per il successo del processo d’impregnazione, infine, si è sottolineato come è necessario che i pezzi arrivino alla fase d’impregnazione perfettamente lavati e privi di contaminanti residui (provenienti dalle lavorazioni meccaniche precedenti, granigliatura e meccanizzazione). È un problema tipico delle aziende che offrono servizi d’impregnazione conto terzi.
Per la preparazione dei materiali, dunque, STS offre la sua gamma di lavatrici rotazionali monostadio multifase, che ottengono la massima efficienza (e grado misurato di lavaggio) utilizzando i formulati acquosi nanotecnologici a base inorganica (bicarbonato) e senza tensioattivi, prodotti dalla stessa azienda. In questo modo non si emulsionano i materiali asportati – inquinando progressivamente il bagno – che invece si separano rapidamente e possono essere allontanati meccanicamente dal formulato , cosa che permette di non cambiarlo mai (se non, precauzionalmente, in occasione delle operazioni di manutenzione ordinaria).
WORKSHOP STS: INSIEME E IN PRESENZA PER ANALIZZARE INSIEME INNOVATIVE TECNOLOGIE
D’IMPREGNAZIONE E RISPARMIO ENERGETICO
Pier Damiano D’Ignazio, direttore marketing e vendite di STS ha scelto, con il sostegno convinto di Ciro Poggioli e l’intera squadra tecnica dell’azienda, una formula originale di presentazione del nuovo impianto Aquasealer©, «studiata per incontrare le esigenze di un pubblico tecnico, molto attento alla qualità dei contenuti degli eventi cui scelgono di partecipare – dice lo stesso Pier – e all’uso più efficiente possibile del tempo, risorsa scarsa da usare con attenzione. Non un compito facile, soprattutto dopo gli anni della pandemia, che hanno disabituato le persone a partecipare in presenza. La formula ha previsto una sessione di workshop della durata di poco più di un’ora e ha dato agli interessati la possibilità di scegliere tra quattro diversi orari ogni al giorno, per un totale di otto sessioni. Per rendere l’esperienza più produttiva – continua Pier – la partecipazione a ogni sessione è stata limitata a un massimo di dieci persone, in modo da agevolare l’interattività. Abbiamo strutturato anche il programma per migliorare la fruizione e ottimizzare l’uso del tempo. I circa cinquanta tecnici e manager di aziende leader nei loro campi d’attività, italiane e multinazionali, hanno potuto vedere dal vivo un impianto d’impregnazione di concezione innovativa in funzione e avuto la possibilità di ottenere risposte a tutti i quesiti posti. Siamo contenti di aver potuto offrire un’esperienza che consideriamo altamente produttiva a gruppi ristretti di specialisti – conclude Pier – che hanno potuto analizzare insieme a noi temi come il risparmio energetico, il controllo elettronico dei processi d’impregnazione, l’efficienza dei nuovi impianti e di processo (gli impianti della serie Aquasealer© consentono un recupero dell’85% della resina non utilizzata ai fini dell’impregnazione), i bassi costi energetici richiesti e, in generale, lo snellimento del flusso logistico e di produzione, in linea con i più recenti sviluppi della lean production».